|
|
|
Eine NC-Drehachse für Modellbauer und Mikrotüftler |
09.02.2012 |
Moin Moin
Nachdem ich mir im letzten Jahr fürs heimische Bastelzimmer noch eine kleine CNC Fräse zugelegt habe,
will ich mit der Maschine natürlich auch Zahnräder und ähnliche, im Teilverfahren gefräste,
Werkstücke herstellen können. Und dafür benötigt man eine zusätzliche Achse, als Drehachse, mit der
man die Werkstücke dann in beliebiger Teilung oder auch mal kontinuierlich rotieren lassen kann.
Gleichzeitig wollte ich eine möglichst handliche Vorrichtung für überwiegend kleine
Werkstückdurchmesser haben, aus dem Grund erschien mir ein umgebauter Vertex HV4 schon zu groß und
auch unnötig schwer für die Fräsmaschine. Außerdem sollen damit auch Kegelräder gefräst werden.
Dafür muss der NC-Indexer, teilweise sehr stark um die vertikale Achse geschwenkt, auf dem
Maschinentisch gespannt werden, was mit den Montageflächen normaler Drehtische schnell sehr
umständlich wird. Nach reiflicher Überlegung habe ich mich dann zu einem kompletten Selbstbau
entschieden.
Bei der Durchsicht meiner diversen "Schatztruhen" fand ich noch einen kleinen 1:110er Schneckenradsatz
aus angelsächsischer Herkunft in der Größe 48DP (entspricht ungefähr einem Modul von 0.53), Zustand
tipp topp und sauber gearbeitet, damit waren dann die Rahmenbedingungen der Konstruktion schon mal
abgesteckt.
Den Grundkörper bildet ein GG25 Block in den Maßen 60x38x38mm, als Spannzangen kommt die Größe ER20
zum Einsatz.
Das vordere Festlager ist ein doppelreihiges Schrägkugellager vom Typ 3804 (20/32/10), am Spindelende
werkelt dann ein einfaches RiKuLa 61903 (17/30/7) als Loslager.
Die Lagerung der Schnecke sitzt als gesondertes Bauteil oben auf dem Kapselgehäuse. Nach anfänglichen
Überlegungen, das Zahnspiel über einen Excenter einzustellbar zu machen, habe ich mich dann aber doch
für eine lineare Verschiebung der Schnecke mittels Langlöchern im Kapselgehäuse entschieden.
Die Gründe hiefür liegen hauptsächlich in meinen Bearbeitungsmöglichkeiten. Mit meinem 16mm
Spindeldurchlass kann ich das 20mm Lagerrohr nicht in die Drehmaschinenspindel schieben, das Bauteil
müsste nun aber von beiden Seiten, in exakt gleicher Excenterstellung, stufenweise ausgedreht werden.
Das ginge nur mit einem exzentrisch hohl ausgebohrten Hilfsfutter, in dem man das Werkstück immer fest
eingespannt lässt und dann damit auch lagerichtig wenden kann. Dieses Hilfsfutter (z.B. ein Zylinder
von ca. 25mm Durchmesser und 80mm Länge) würde ich aber noch nicht mal durchs Futter bekommen. Also
gibt's diese Langlöcher, das ist nicht ganz so elegant, funktioniert aber auch einwandfrei.
Den Antrieb übernimmt ein kleiner NEMA17 Schrittmotor von Nanotec.
Nach den Fräsarbeiten am Kapselgehäuse für das Schneckenrad...
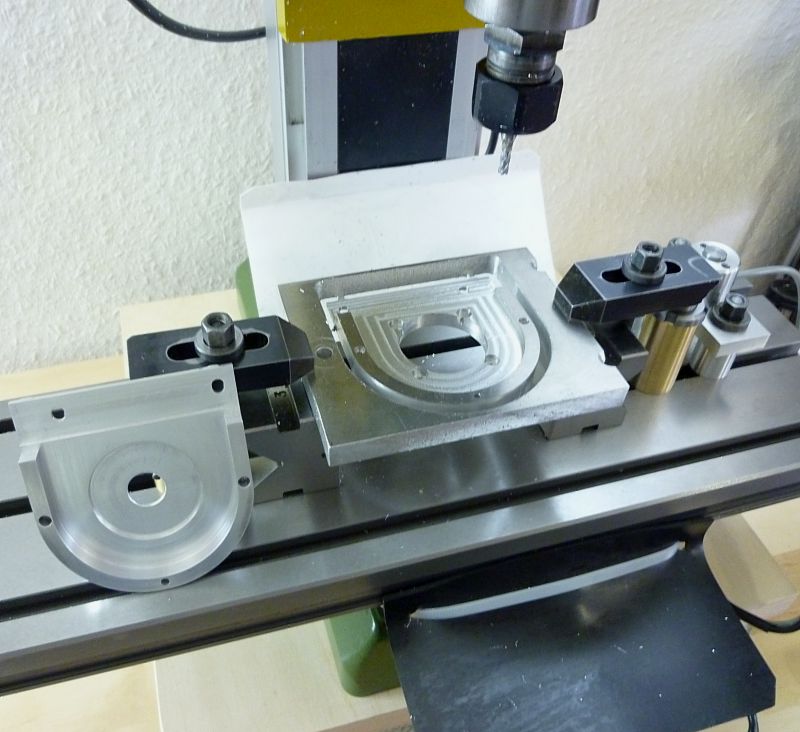
...konnte der Hauptlagerblock und die Spindel in Angriff genommen werden.
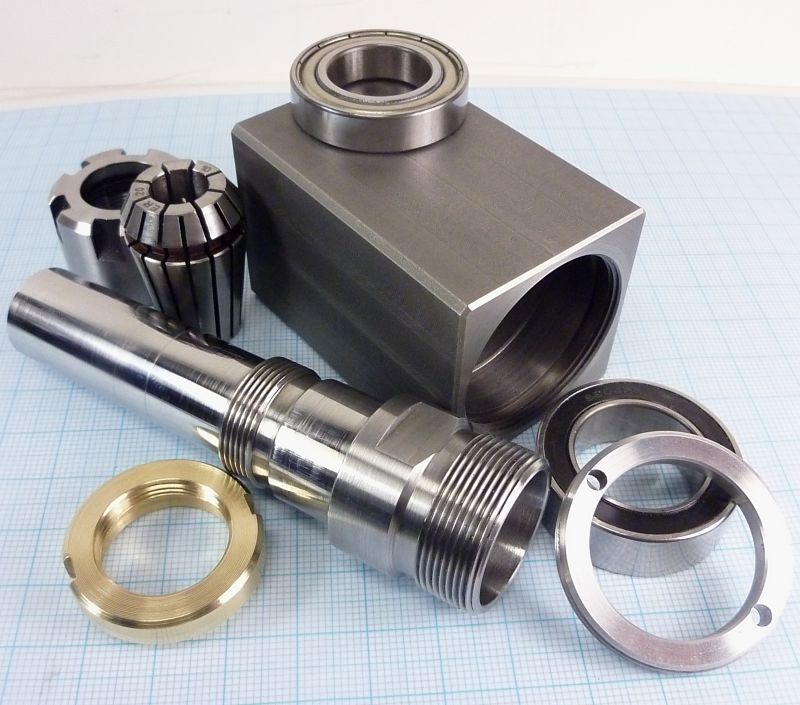
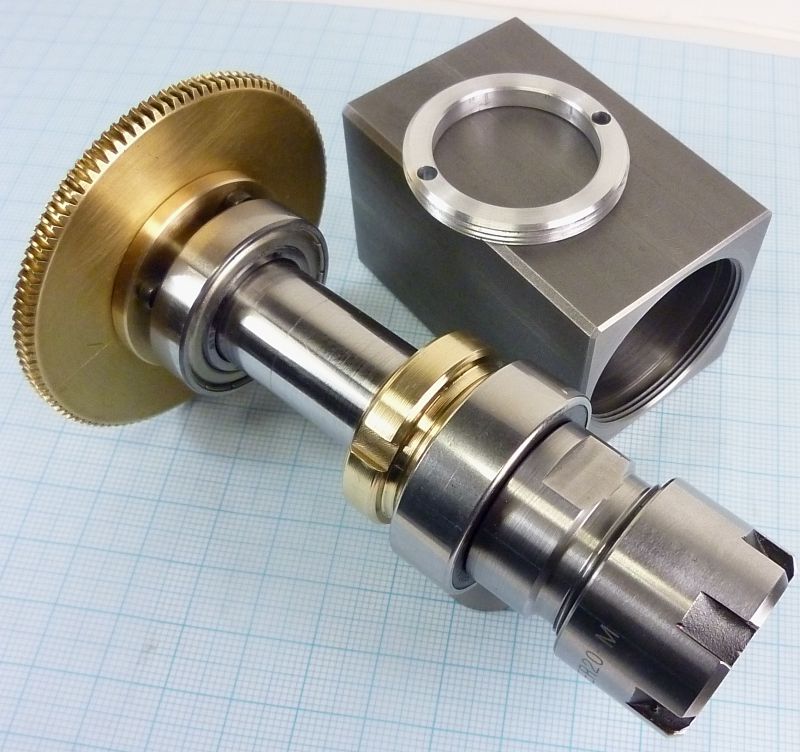
Das Schneckenrad, welches von Haus aus eine 6.35mm Achsbohrung aufwies, wurde in einem exakt zentrisch
laufenden Hilfsfutter (dabei vollständig am Umfang der Zähne gespannt) auf 21mm ausgedreht und erhielt
anschließend einen neuen Achsadapter mit geschlitztem Spanneinsatz.
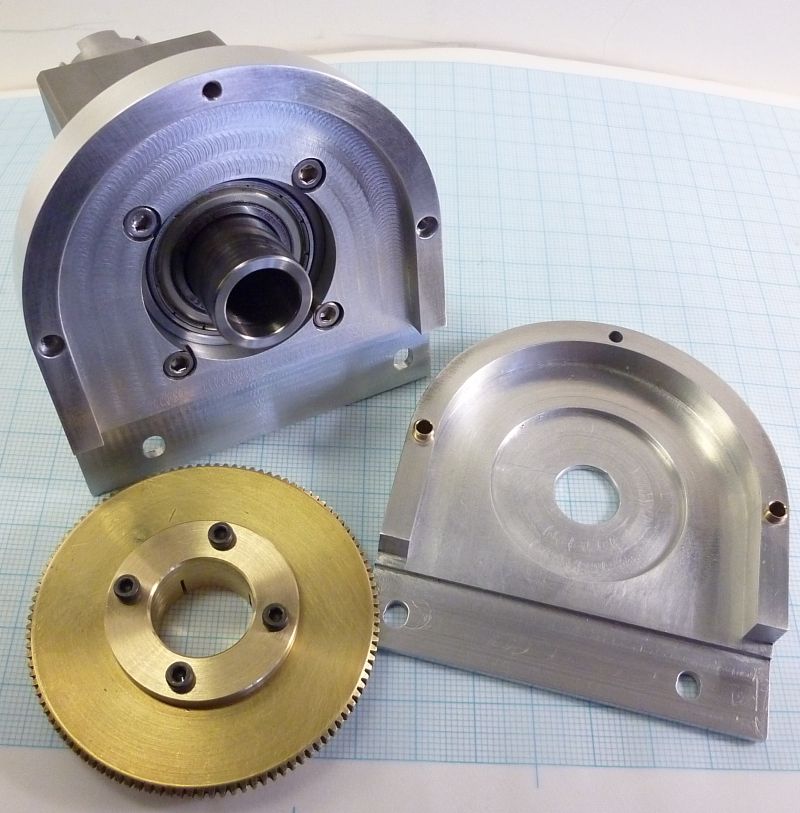
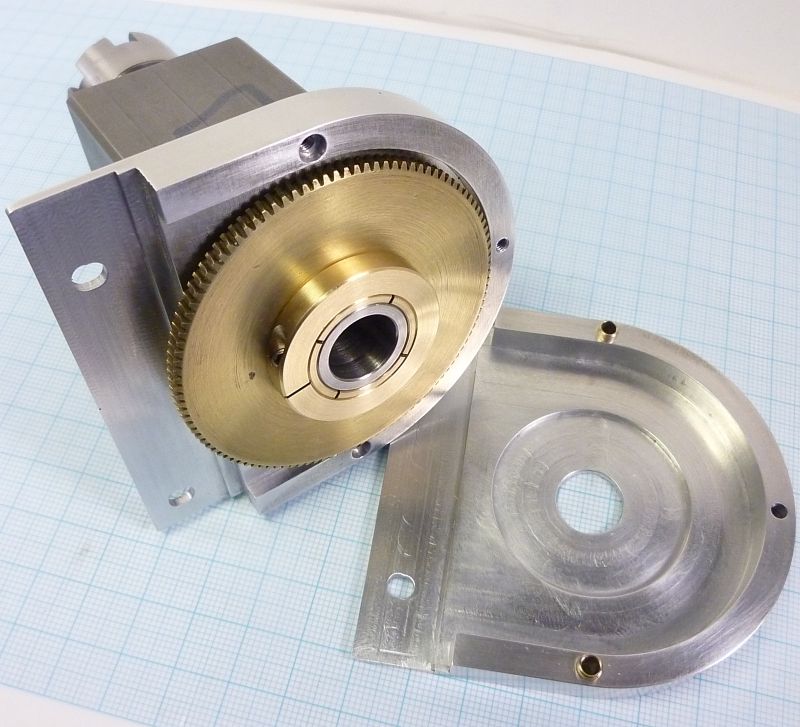
Und hier das Innenleben der Scheckenlagerung mit eigens angefertigter Wellenkupplung, sowie das
Lagergehäuse mit dem Motorflansch.
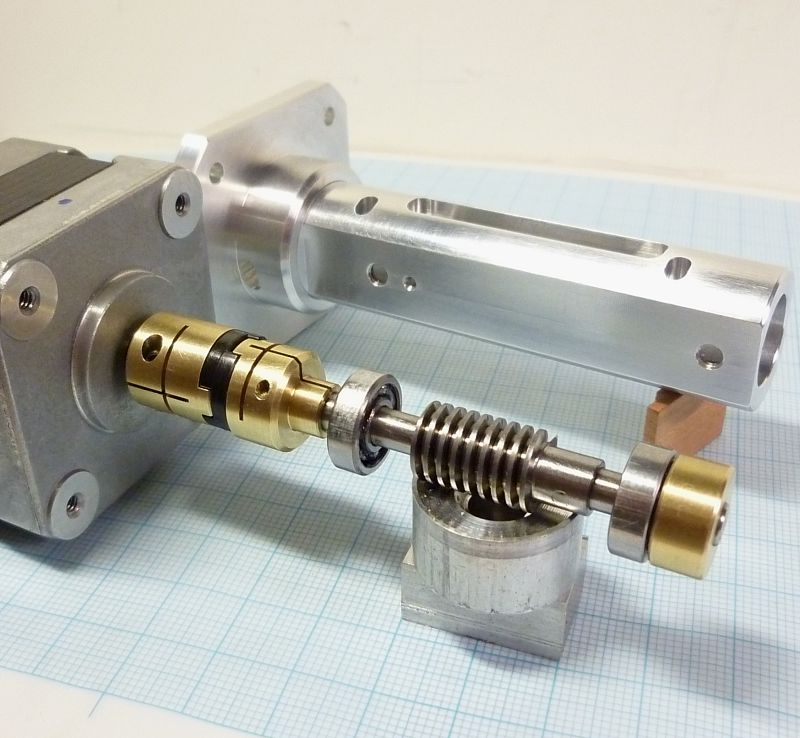
Da man an einer demontierbaren Vorrichtung keine feste Verkabelung haben will, benötigt man natürlich
noch eine Steckkupplung, welche auch noch in ein stabiles Gehäuse gepackt werden muss.
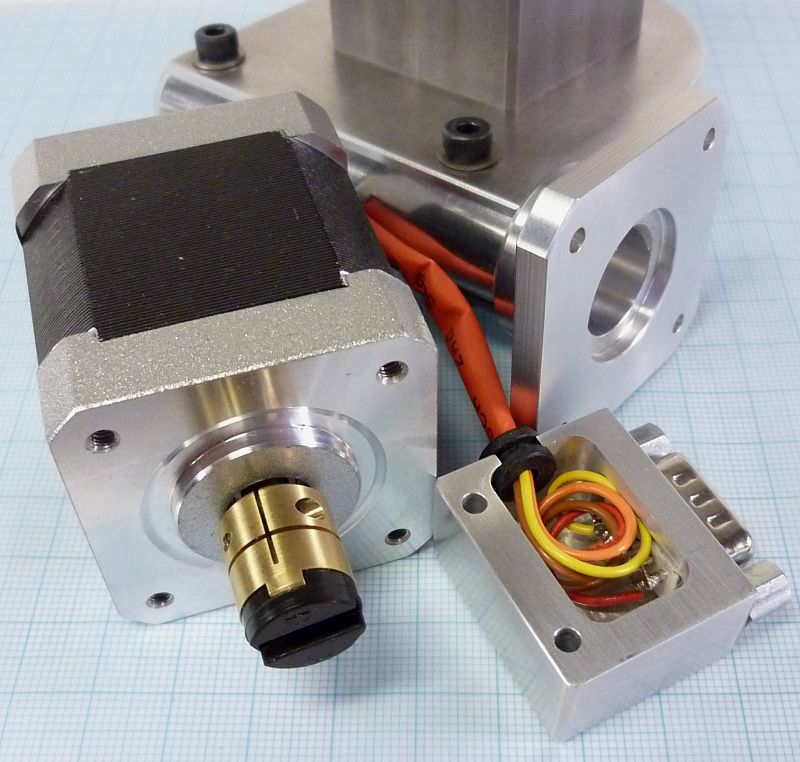
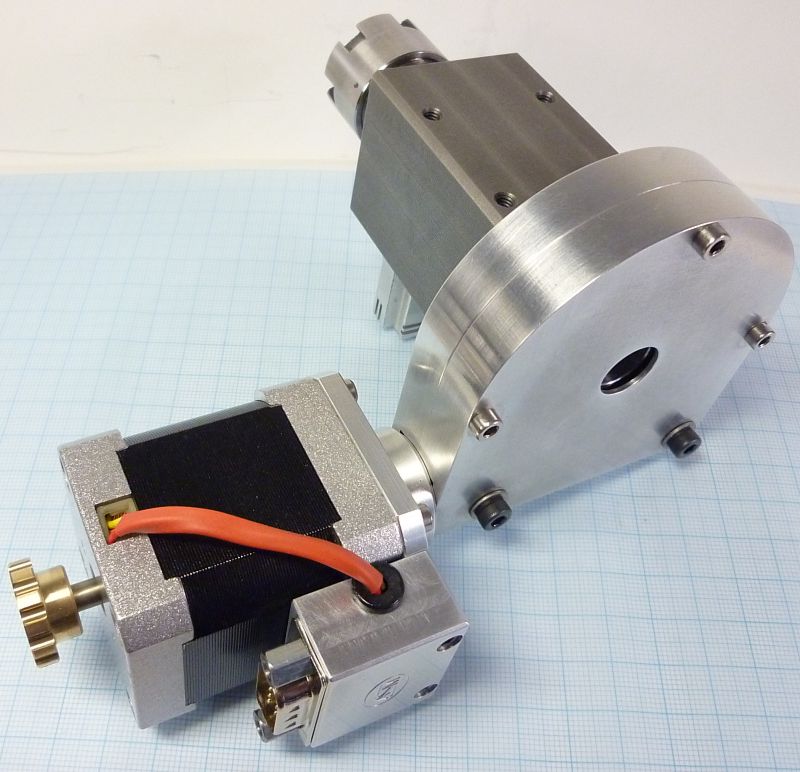
Nun braucht der Grundkörper nur noch einen stabilen Standfuß, vorzugsweise gleich als Drehteller
ausgebildet, dann ist der kleine NC-Indexer eigentlich schon fertig.
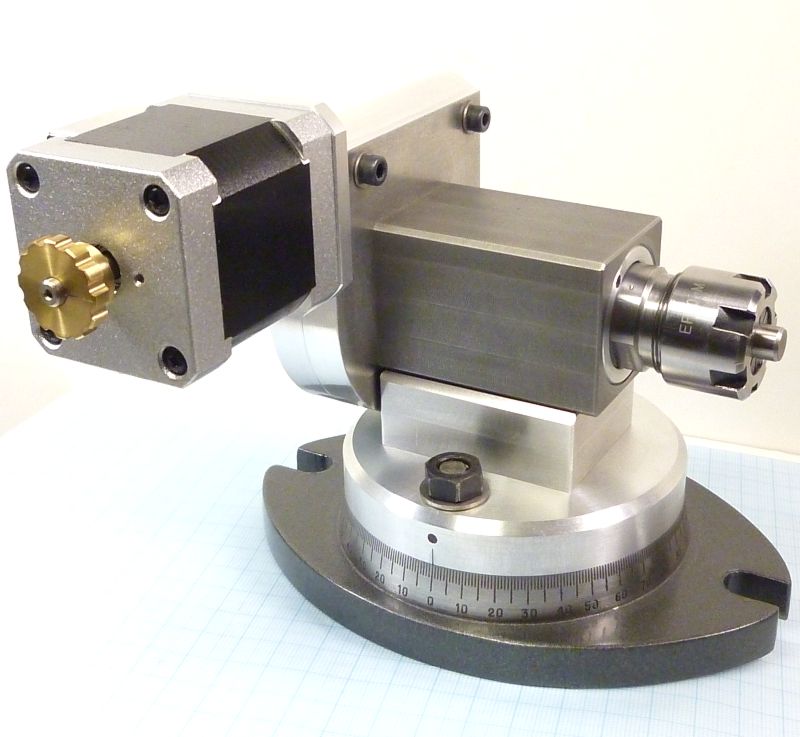
An dieser Stelle schon mal ein Video von den ersten Testläufen, hier noch mit einem Schraubstock als
Hilfseinspannung des Gerätes.
Testlauf A-Achse
Und noch mal eine Zusammenfassung der Eckdaten:
- Werkzeugspindel ER20, Rundlaufgenauigkeit im Gesamtsystem kleiner 0.01mm
- Stepper Nanotec NEMA 17, ST4118L-3004, 3A, 0.5Nm, 1.8grd/St
- Schneckengetriebe Modul 48DP (ca. m0.55), i 1:110
- Ansteuerung im 10tel Schrittbetrieb
- Max. Drehzahl der NC-Achse (G0 im 10tel Step-Mode) 9.5 U/min (1045 U/min Motordrehzahl)
- Max. Winkelgeschwindigkeit der NC-Achse 3420grd/min
- Winkelauflösung im Vollschritt 0.0164grd (ca. 1'), im 10tel Schritt Betrieb 0.0016grd (ca. 6")
Gemessenes Zahnflankenspiel (Umkehrspiel) der NC-Achse:
Kleiner 0.01mm an einem Arm mit 50mm Radius, das entspricht einem Winkel kleiner 0.01grd. Bei einer
für mich üblichen Werkstückgröße im Durchmesser um 20mm, bedeutet das einen Umkehrspielfehler in der
Größenordnung von 0.002mm auf der Manteloberfläche des Zylinders.
Wie Ihr mittlerweile wohl alle wisst, tue ich mir, auf Grund meiner Mini-Maschinen Ausstattung, immer
etwas schwer mit der kompletten Anfertigung großvolumiger Stahl- oder Gussteile. Deswegen habe ich
hier den Fuß eines kleinen, drehbaren Schraubstockes, als Basis für meine Konstruktion,
zweckentfremdet. Der passt prima in der Größe, ist stabil und eine zirkulare T-Nute ist auch schon
drin. Ist natürlich nicht ganz so elegant, wie eine vollständige Eigenkonstruktion.
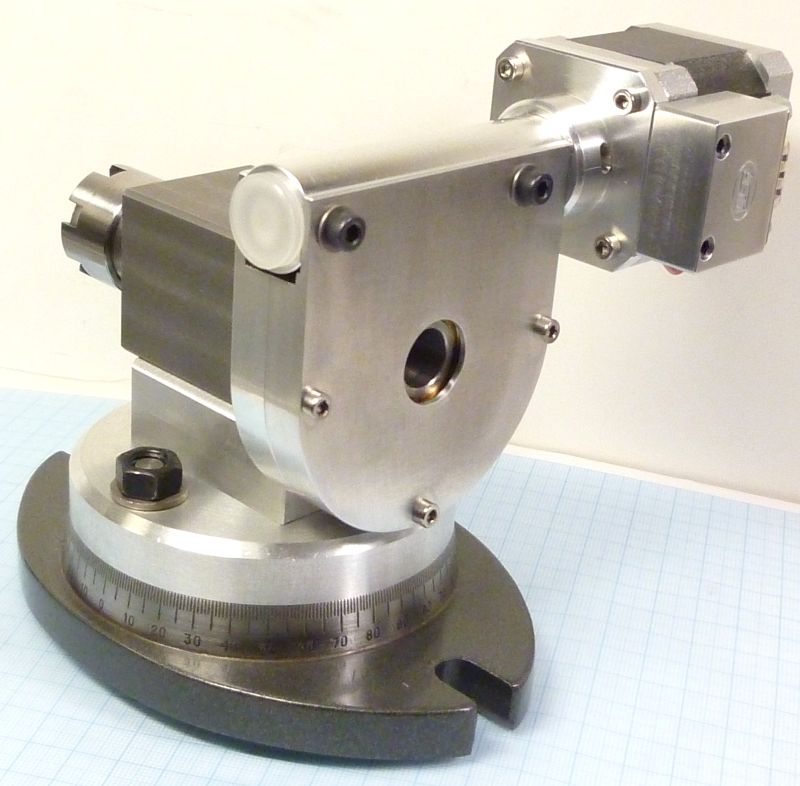
Die vom "Fernostmann" gestoßene Gradskala ist zwar nicht gerade eine Augenweide, aber sie ist in der
Teilung präzise ausgeführt und genügt somit für meine Zwecke.
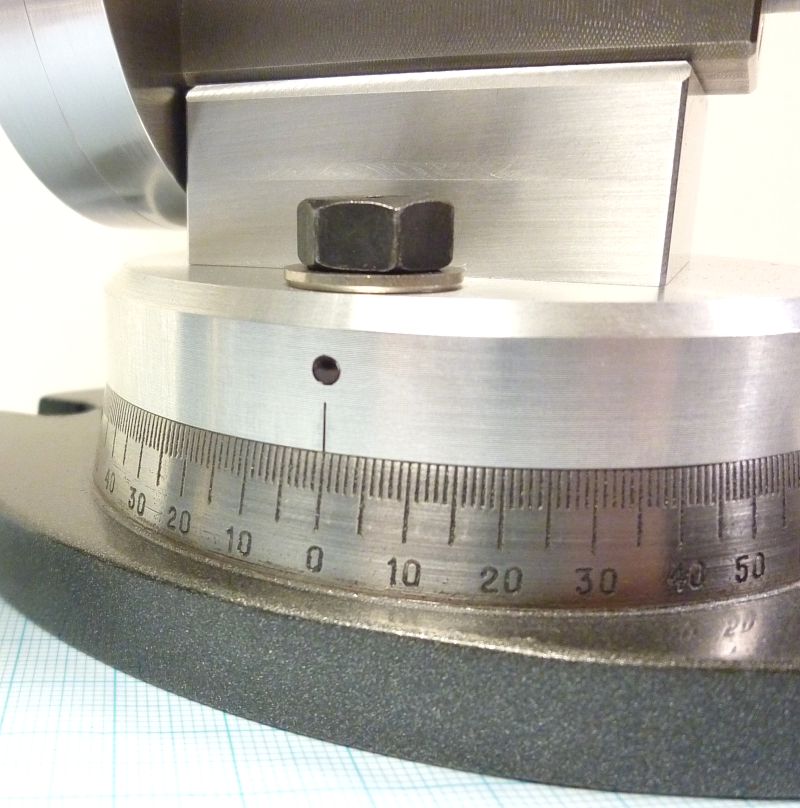
Zum Abstützen längerer und empfindlicher Werkstücke braucht man natürlich noch einen Reitstock. Die
meisten, am Markt erhältlichen, Geräte sind für meinen Zweck leider viel zu klobig, und die Wenigen,
welche gerade noch so gepasst hätten, waren mir zu primitiv, deswegen ging am Selbstbau mal wieder
kein Weg vorbei, ist ja klar... ha ha ha....
Damit ich das Teil auch zusammen mit meinem Vertex HV4 Drehtisch einsetzen kann, musste ich ihn
höhenverstellbar auslegen, deswegen gestaltete sich der Aufbau doch ein bissel aufwändiger.
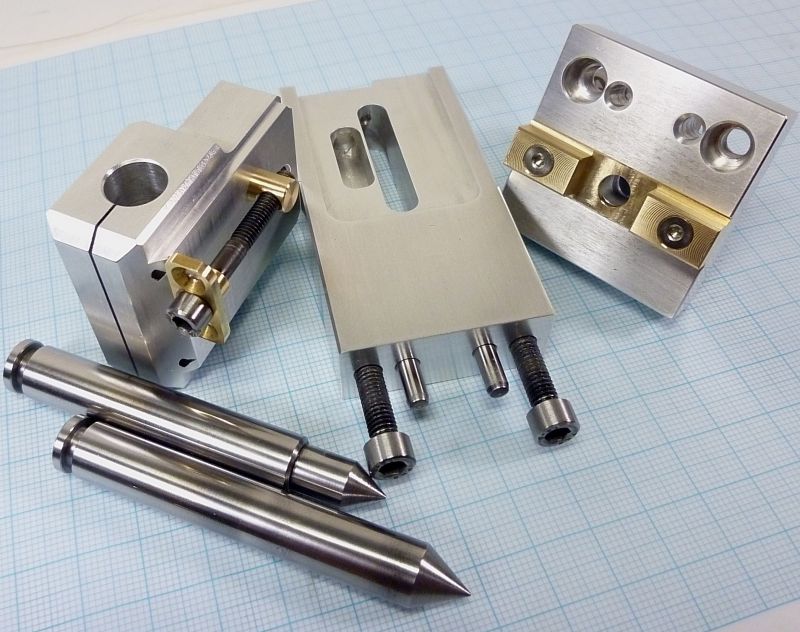
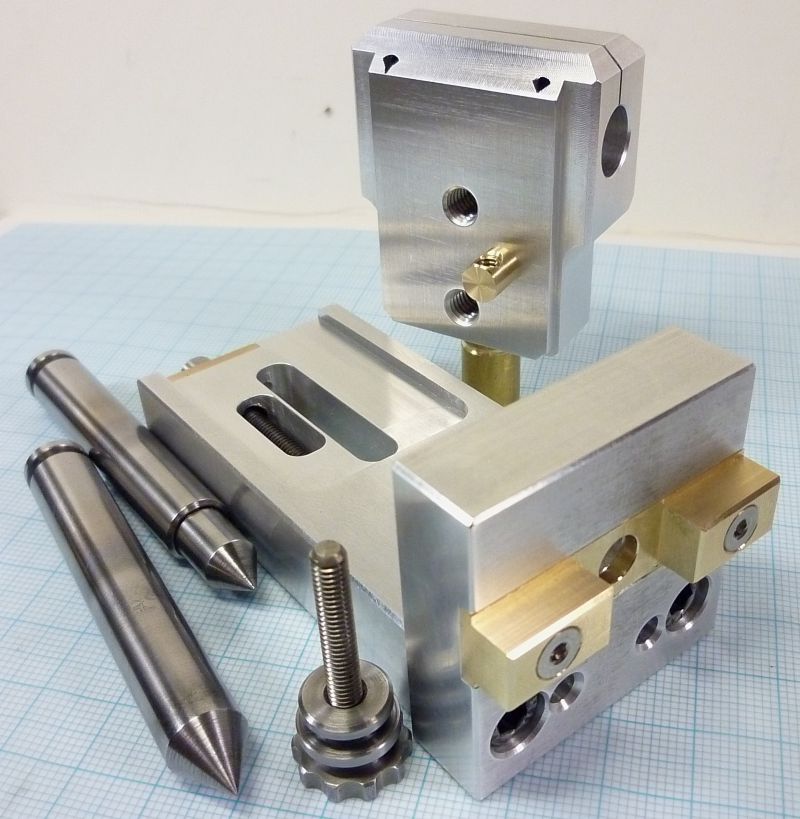
Nach dem Lösen der beiden rückwärtigen M6er Klemmschrauben kann man das Oberteil, mit Hilfe der
senkrechten M4 Spindel, rauf- und runterkurbeln, der Verstellbereich der Spitze geht von 75 bis 83mm.
Die Zentrierspitzen wurden aus 10mm Silberstahl hergestellt und sind im Spitzenbereich gehärtet.
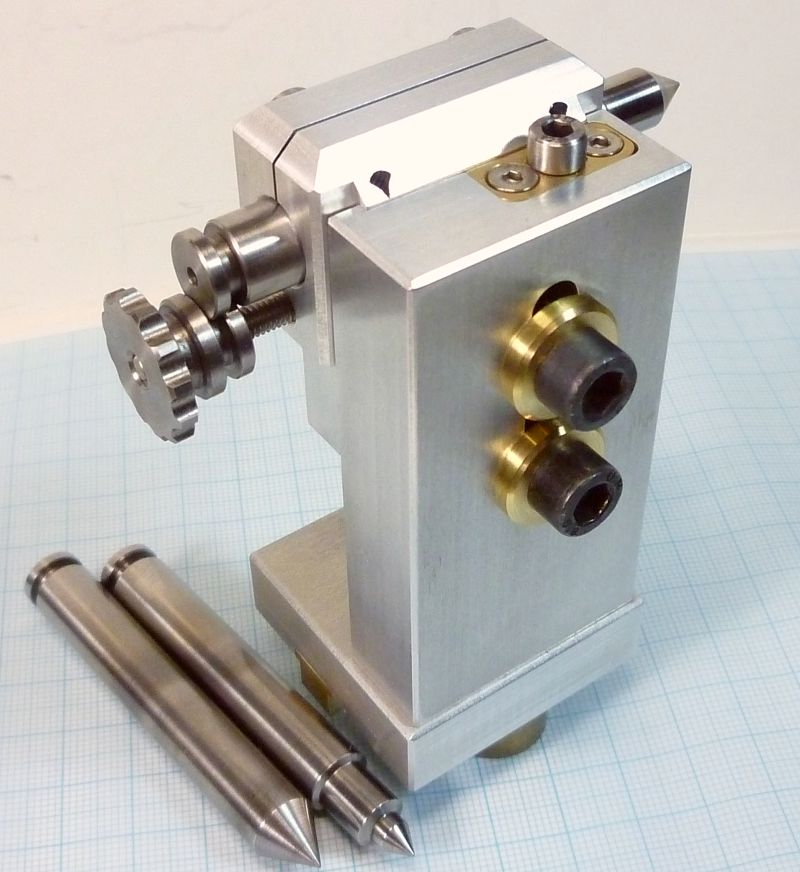
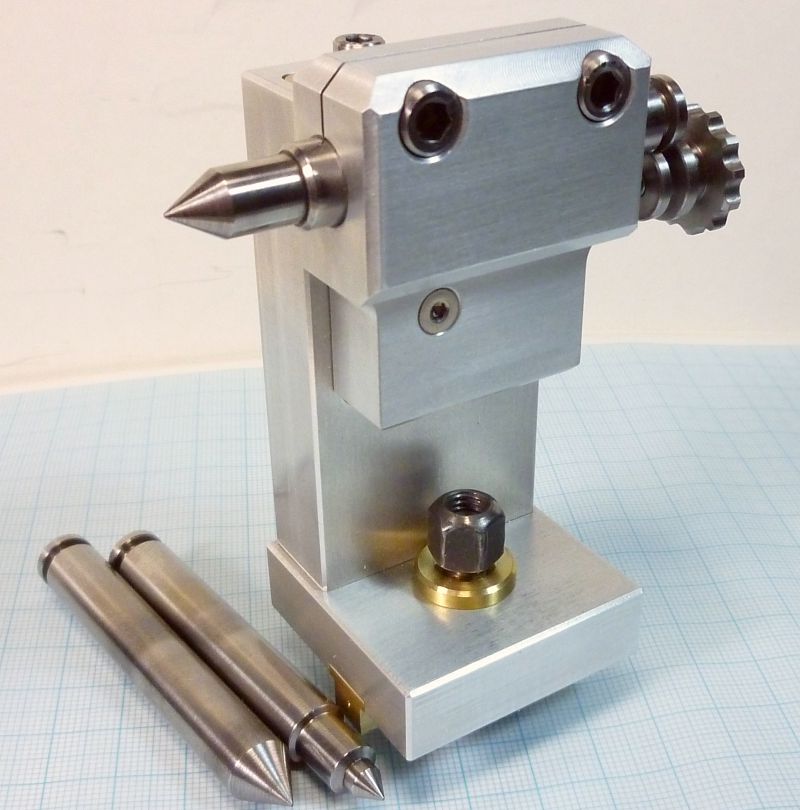
Und so sieht das ganze Ensemble dann auf dem Maschinentisch der Proxxon FF500 aus.
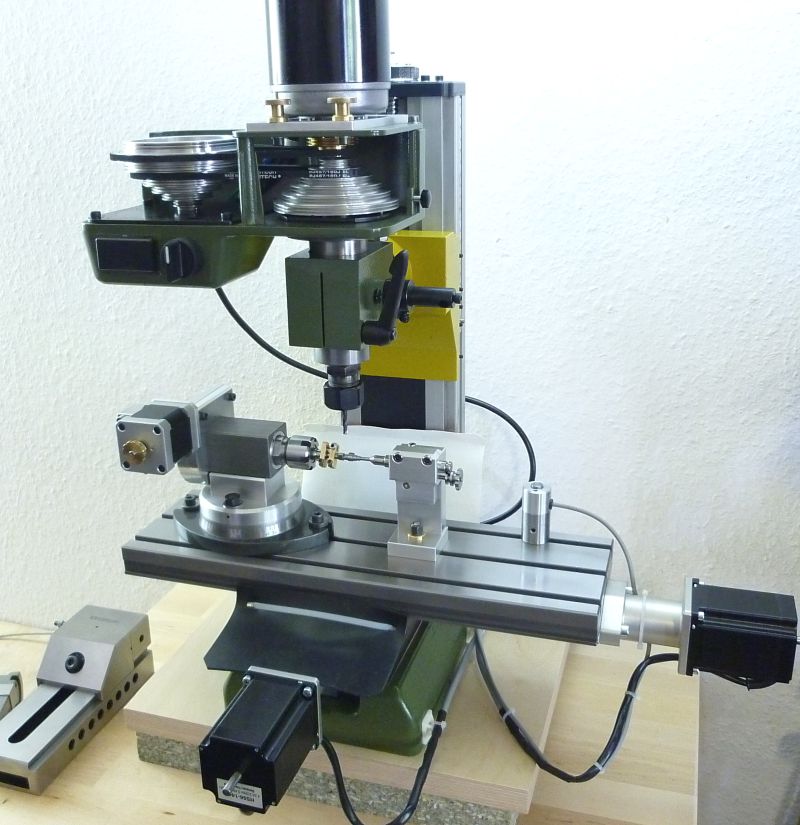
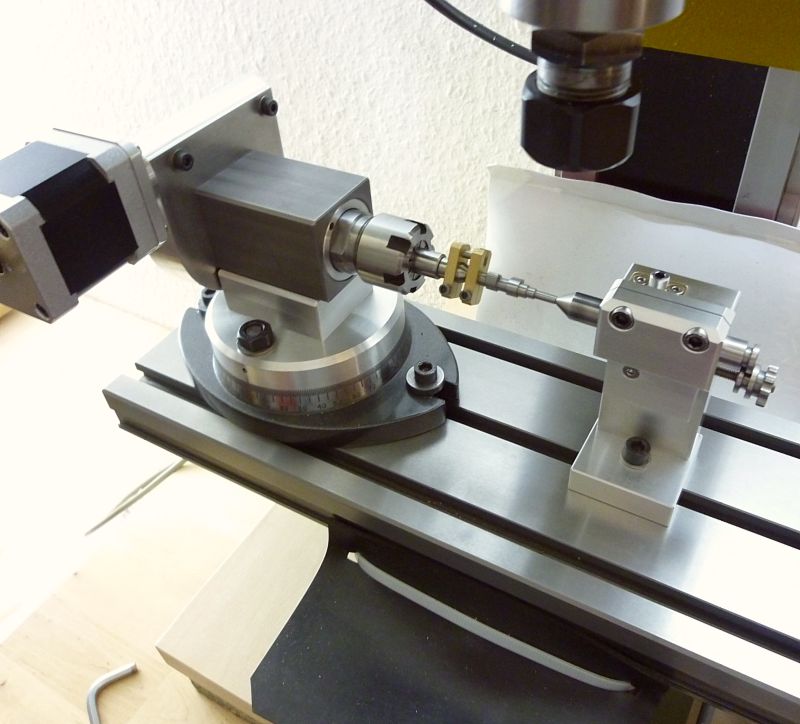
Okay, zum Schluss noch ein paar Beispiele, was man mit dem Teil in der Praxis alles anstellen kann.
Man kann damit z.B. nette Steuerkurven fräsen...
FF500 Mantelfräsen mit Drehachse
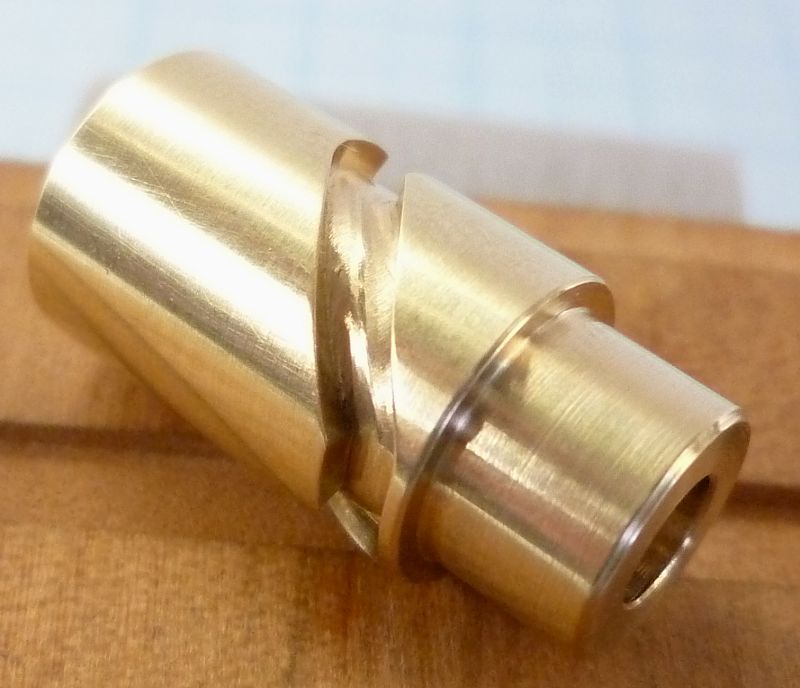
...oder auch alles Mögliche auf einen Zylindermantel gravieren.
FF500 Gravieren mit Drehachse
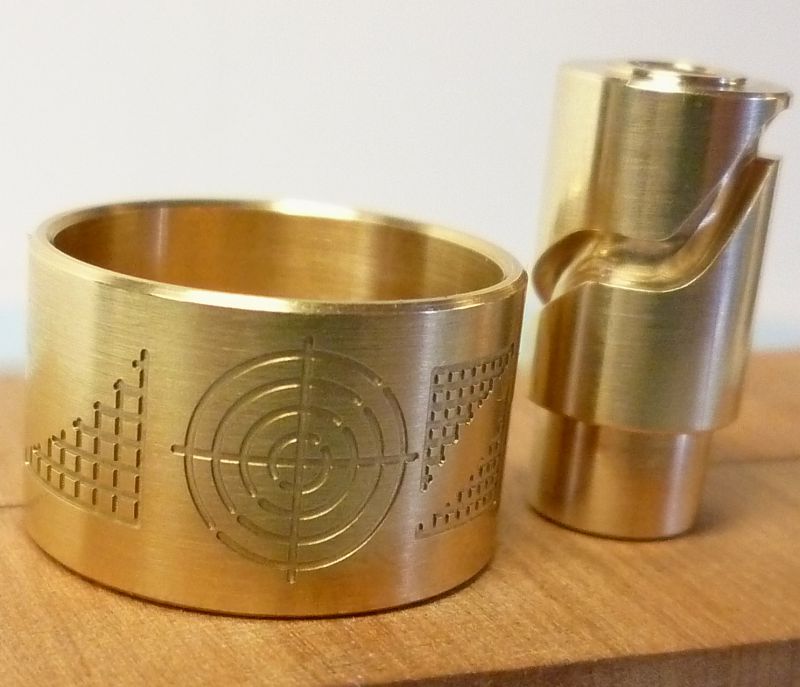
Zum Gravieren mit kleinen Stichelen (ich arbeite auch mit Stichelbreiten von 0.1mm) braucht man hohe
Drehzahlen. Ich kann zwar, aufgrund eines Vorgelegeumbaus, mit der originalen Spindel der FF500 schon ca.
5000 U/min fahren, aber ein bissel mehr Touren wären für randscharfe Ergebnisse doch erheblich
günstiger.
Für diesen Zweck habe ich mir eine Montagebrille, passend zu einer meiner kleinen Schleifspindeln,
angefertigt.
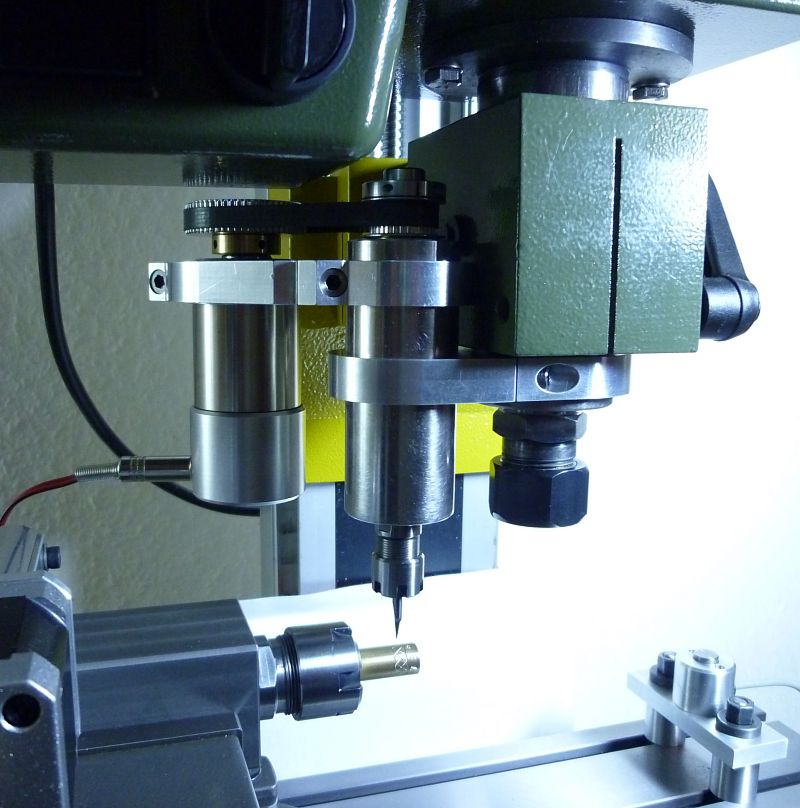
So kann ich die Spindel schnell und problemlos einwechseln, der 50mm Wegverlust in X stört beim
Gravieren der, in der Regel kleinen, Bauteile eigentlich nicht weiter.
Mit dieser Annordnung habe ich dann 12tausend Touren mit einem 55 Watt Motörchen, das reicht absolut
und funktioniert zum Gravieren bestens.
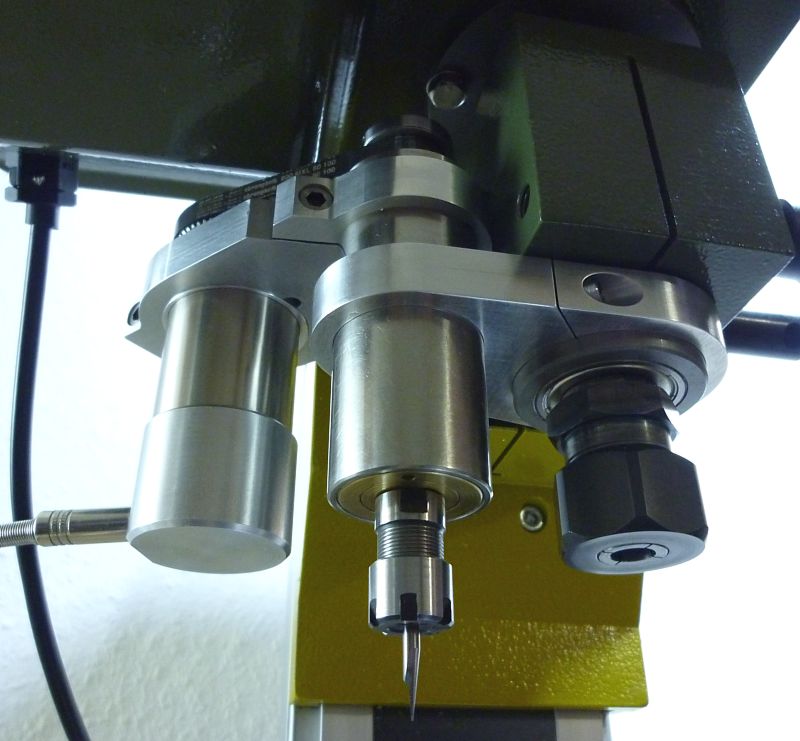
Kommen wir zum zweiten Haupteinsatzgebiet meiner Drehachse, dem Zahnradfräsen.
Ich meine damit aber nur die einfache Herstellung mit einem Formfräser (z.B. Modul Scheibenfräser) im
Teilverfahren und kein Abwälzfräsen, bei dem sich Drehachse und Werkzeugspindel in einer
synchronisierten Abhängigkeit bewegen müssten.
Bei mir steht also bei der Bearbeitung das Werkstück still und der Formfräser wird am Umfang axial
vorbei gefahren, genau so, wie man es auf der handgekurbelten Fräse mit einem Teilapparat auch
machen würde. Nur braucht man mit der CNC Maschine nicht hundertmal hin und her kurbeln und dauernd
den Teilapparat weiterdrehen, man kann, während die Maschine läuft, gemütlich Kaffee trinken
gehen... ha ha ha....
Der praktische Aufbau sieht dann bei mir in etwa immer so aus.
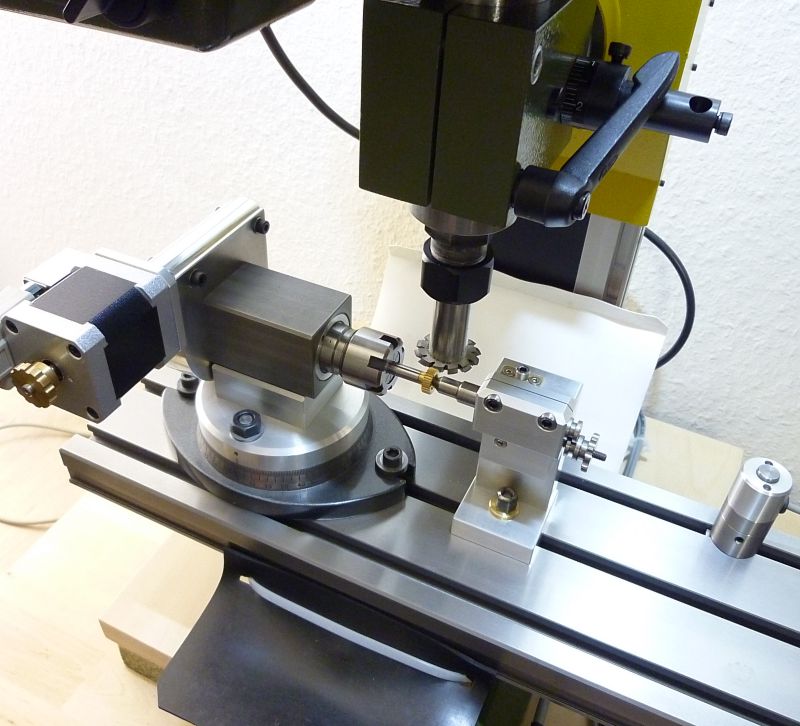
Nun haben die bezahlbaren CAM Systeme für Hobbyisten (ich benutze im Moment für die meisten 2.5D Jobs
SheetCam) keine Routinen für die hier benötigten Bewegungsabläufe. Und ich verspürte wenig Lust, für
jedes Zahnrad den G-Code mühselig selber zu schreiben, bei 48 Zähnen und 5 bis 6 Durchgängen pro Zahn
kommen da schon eine ganze Menge Zeilen zusammen.
Da ich leider von Programmierung nichts verstehe, war der Hans so nett, ein kleines Tool zu
entwickeln, mit dem man den jeweiligen G-Code sehr bequem und schnell erstellen kann.
Das Programm myCam, welches in unserem Servicebereich zur freien Nutzung zur Verfügung steht,
erzeugt G-Code für Maschinensteuerungen unter Mach3 und funktioniert bei mir einwandfrei, mit anderen
Systemen wurde es aber nicht getestet!
Als Voraussetzung wird angenommen, dass die Drehachse in der Steuerung als A-Achse und mit den
Winkeleigenschaften "A360 entspricht einer vollen Umdrehung" definiert ist. Die Z-Achse kann für den
eigentlichen Fräsprogrammlauf vollkommen deaktiviert sein, sie wird dabei nicht angesprochen. Wer
also weiterhin nur einen 3-Achs Controller verwendet, könnte in einem gesonderten Mach3 Profil die
Achsen umdefinieren (die Z-Endstufe wird dann für A verwendet) und trotzdem den NC-Indexer ansprechen.
In den Fällen muss man vorher im originalen "Mach3 Fräsen Profil" die Z-Höhe des Modulfräsers auf die
Mitte der Teilspindel einrichten, dort stehen lassen, anschließend in Mach auf das spezielle
Profil zum Zahnradfräsen umschalten und dort dann den Programmcode laden.
Der erzeugte G-Code arbeitet nach folgendem Schema:
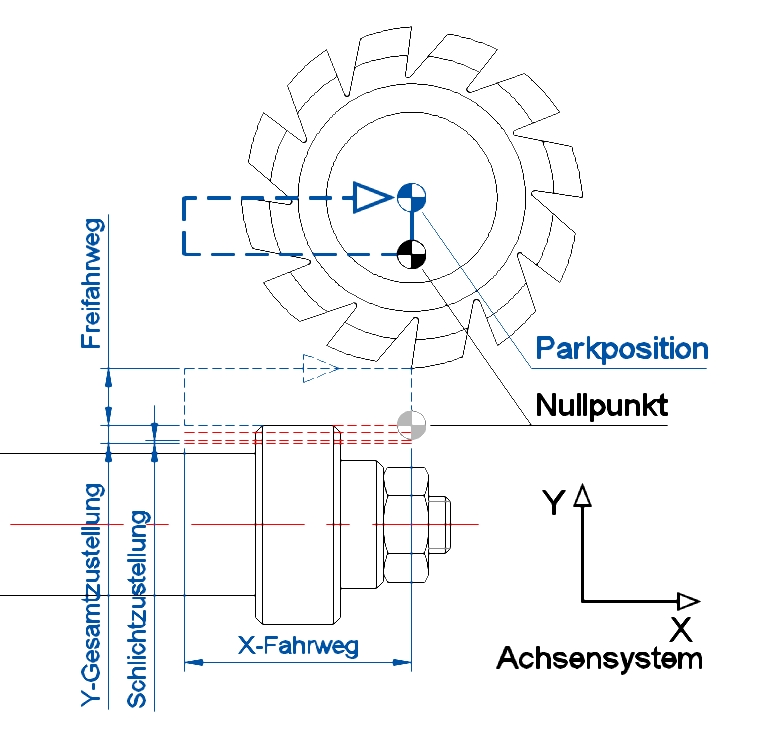
Das Werkzeug fährt aus dem Nullpunkt zunächst in die Parkposition und die A-Achse dreht
das Werkstück auf 0grd. Anschließend kommt es zu folgender Iteration:
1. Das Werkzeug wird um die jeweilige Schrupp- bzw. Schlichtzustellung addiert, in Y- verfahren.
2. Es fährt eine Arbeitsfahrt, also einen Fräsdurchgang, in X- am Werkstück entlang.
3. Es verfährt um den Freifahrtweg Y+ vom Werkstück weg.
4. Es setzt um X+ zurück auf die Parkposition.
Das wiederholt die Routine solange, bis die volle Frästiefe des Zahnprofils erreicht ist
und dreht dann die A-Achse zum nächsten Zahn weiter. Nach Fertigstellung aller Zähne bleibt die
Maschine in der Parkposition stehen.
Der Maschinennullpunkt (und damit der Startpunkt der Zyklen) liegt, bezogen auf den Y Wert, auf der
Mantelfläche des Räderrohlings. Das ermöglicht das einfache Einrichten des Fräsers auf das Werkstück.
So kann man z.B. mit laufender Frässpindel vorsichtig am Rohling ankratzen und dann das DRO für
Y in der Maschinensteuerung auf Null setzten. Danach fährt man mit der Spindel in X einige Millimeter
nach rechts und nullt dort das DRO für X.
Nun braucht man für den X-Fahrweg nur noch diese Vorstrecke, die Bereite des Zahnrades und eine kleine
Überfahrstrecke hinter dem Zahnrad zu addieren und als -X Wert im Programm eintragen. Dabei muss
bezüglich der Länge der Überfahrstrecken natürlich immer eine eventuelle Kollision mit dem Futter
und/oder dem Reitstock beachtet werden!
Die Zustellungen in das Zahnprofil werden als Y Minuswerte angegeben, also muss bei einer
Gesamtprofiltiefe von 0,5mm, unter "Y-Gesamtzustellung / Schnitttiefe", hier "-0,5" eingetragen werden. Die
Zustellwerte für die Schruppgänge und den Schlichtgang können in vorteilhafter Weise einzeln
definiert werden. Mit "Y-Schruppzustellung" legt man den max. Zustellwert für den einzelnen
Schruppgang fest, die jeweilige Anzahl der Schruppgänge wird vom Programm in den kompletten
Schruppzustellweg (Gesamtzustellung - Schlichtzustellung) eingeschachtelt. Die Schlichtzustellung
kann somit, unabhängig von den Schruppgängen, als gesonderter Wert eingetragen werden.
Nach der Eingabe des Fräsvorschubs, gibt's zum Schluss noch die Möglichkeit, den Eilgang individuell
zu gestalten. Neben dem üblichen G00, welches fest in der Maschinensteuerung abgelegt ist, kann man
somit eine eigene Frei- und Rückfahrgeschwindigkeit definieren. Auf diese Weise können sich die
Zyklen langsamer und damit auch etwas leiser ablaufen lassen. Das mag für die Meisten wohl
uninteressant sein, so Wohnungszerspaner wie ich brauchen so was schon mal, einfach um auch gegen
22Uhr noch schnell mal ein Rädchen fräsen zu können....ha ha ha...
Ein üblicher Programmablauf sieht dann wie in dieser Demo hier aus:
Ablauf eines mit myCam erstellten Programmes
Zum Schluss noch ein konkretes Beispiel aus der Fertigung.
Die Planung eines neuen Modellverbrenners mit Ventilsteuerung via Königswelle, erzeugte bei mir einen
gewissen Bedarf an speziellen Kegelrädern. Räder mit dem Übersetzungsverhältnis 1:2 sind in Modulen
kleiner 0.5 fast nicht erhältlich, und wenn dann nur mit so großen Zähnezahlen, dass sie trotz kleinem
Modul gleich wieder viel zu groß für meine Zylinderkopfgestaltung wurden. Also habe ich zur besseren
Weiterplanung mal ein Musterpärchen aus Messing in meiner Wunschgröße m0.4 12/24Z hergestellt.
Geradverzahnte Kegelräder werden üblicher Weise auf Verzahnungsmaschinen mittels Abwälzstoßen
hergestellt, dabei bleibt das Modul nicht konstant, sondern verjüngt sich zur Kegelspitze hin. Diese
Möglichkeit der Fertigung hat man mit einem einfachen Modul Formfräser leider nicht. Um wenigstens zu
einigermaßen brauchbaren Ergebnissen zu kommen, kann man aber ein so genanntes "Hilfsverfahren
zur Kegelradherstellung auf der Universalfräsmaschine" anwenden. Hierbei werden nach dem mittigen
Hauptfräsgang der Zahnlücke, noch zwei weitere Fräsgänge mit leicht verdrehter Teilspindel, ober- und
unterhalb der Profilmitte, absolviert. Die Kopf- und Fußbahnen laufen dann parallel und schneiden sich
nicht in der gemeinsamen Kegelspitze, dabei ergibt sich über die ganze Zahnbreite die gleiche
Zahnhöhe.
Die so erzeugten Kegelräder weisen natürlich kein perfektes Tragbild auf. Da bei meinem Einsatzzweck
die Belastungen aber nicht allzu groß ausfallen, wollte ich es doch gerne mal damit versuchen. Die
Zeichnung für mein Räderpärchen sieht so aus:
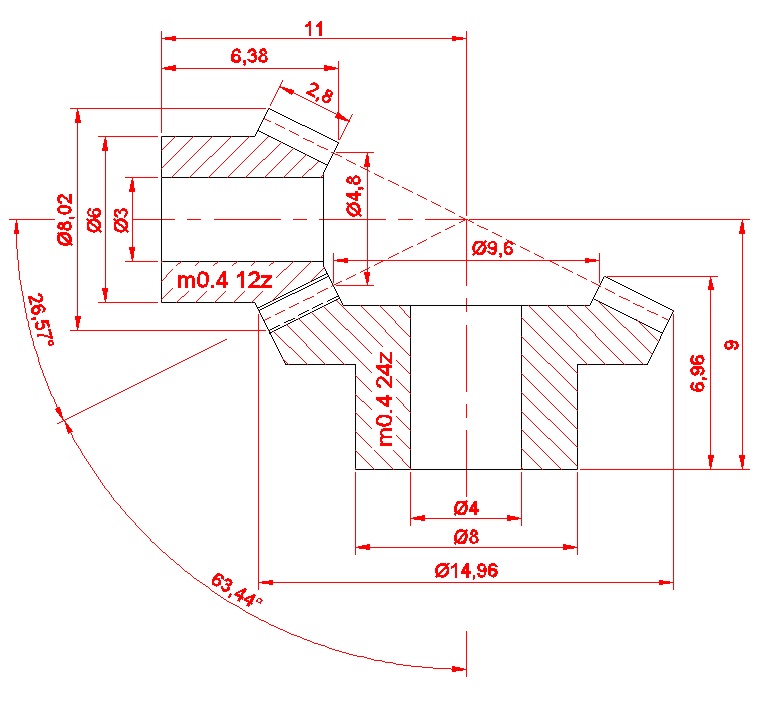
Die Anfertigung der Räderrohlinge habe ich auch gleich auf der, kurzzeitig zur improvisierten CNC
Drehe umgerüsteten, Fräse erledigt. So wird's präzise und man spart sich einen Haufen Zeit, die man
sonst, fürīs möglichst genaue Einrichten des Obersupports auf die vier verschiedenen Kegelwinkel,
aufbringen müsste.
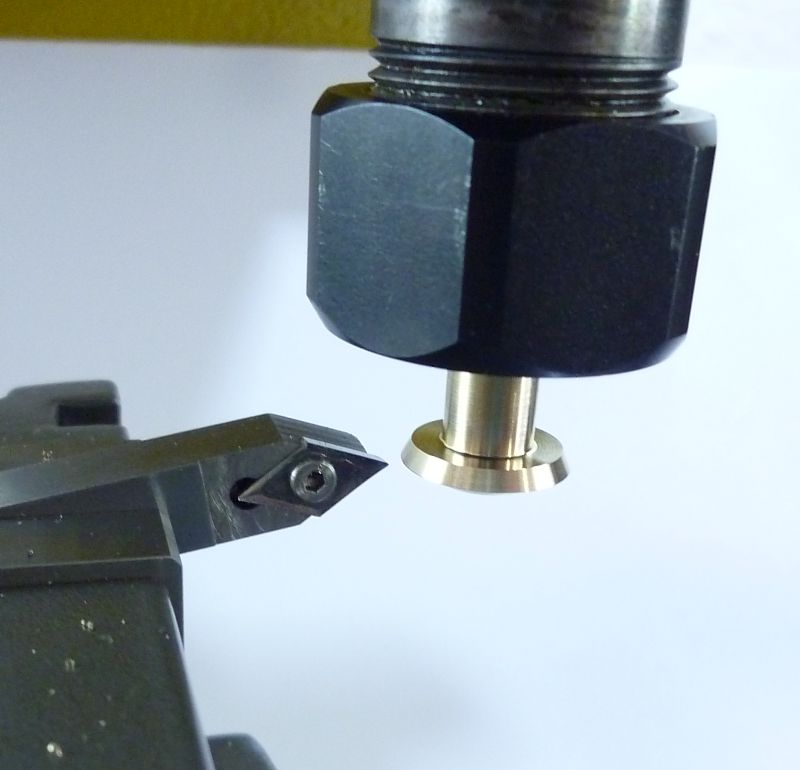
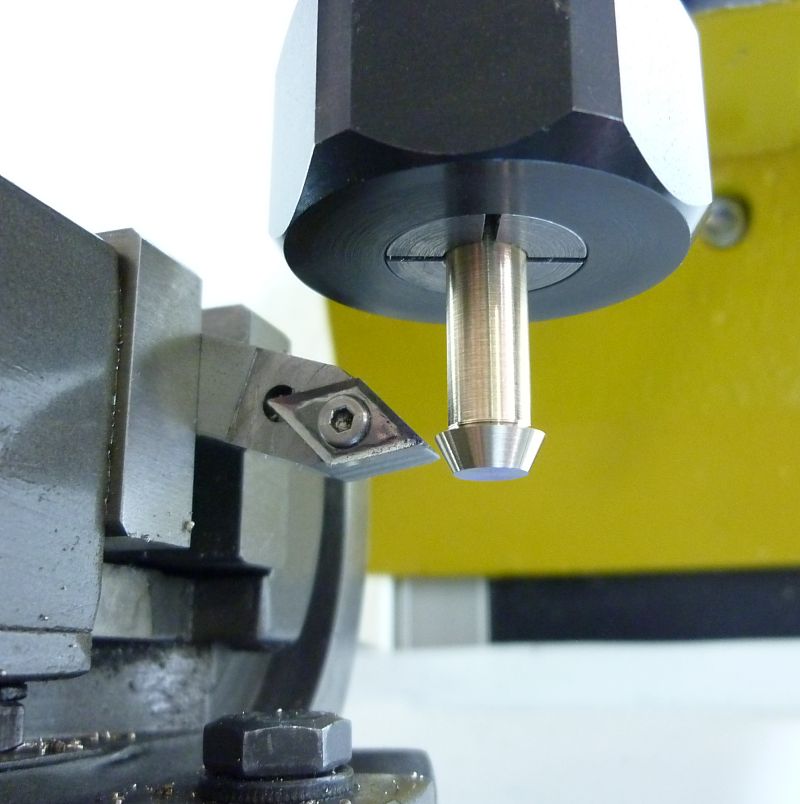
Das Ganze noch mal im Video
Kegelrad Rohling Drehen
und die fertigen Rohlinge.
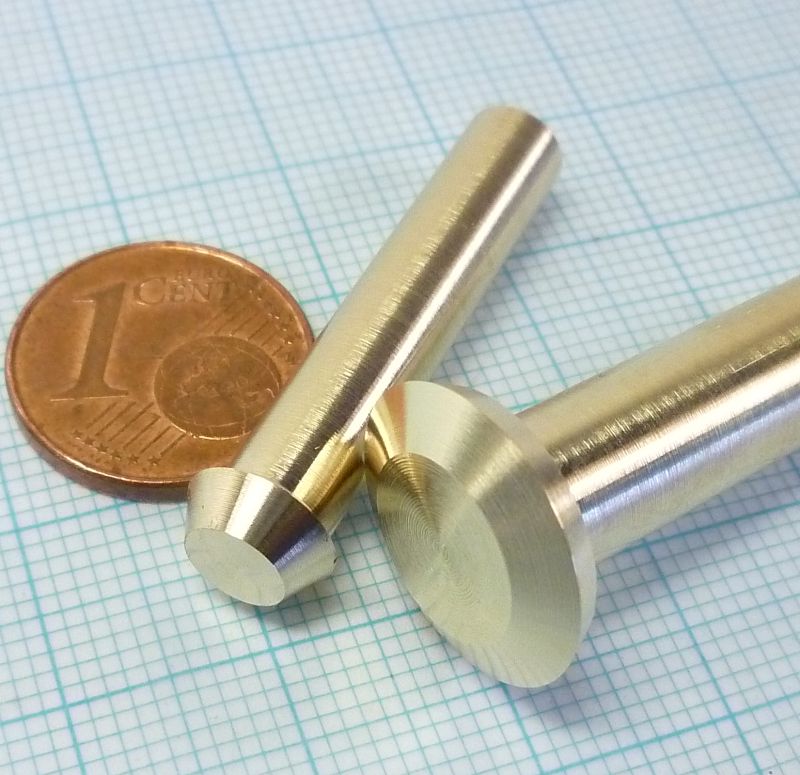
Dann ging's ans Fräsen.
Die Bilder zeigen die NC- Drehachse in einem Schraubstock gespannt, das war noch in der Bauphase, als
der endgültige Drehtellerfuß noch nicht fertig angebaut war. Deswegen musste hier der Schraubstock,
mit Hilfe des Winkelmessers, in die jeweiligen Kegelwinkel geschwenkt werden, das kann ich nun mit
der Skala am Montagefuß einfacher erledigen.
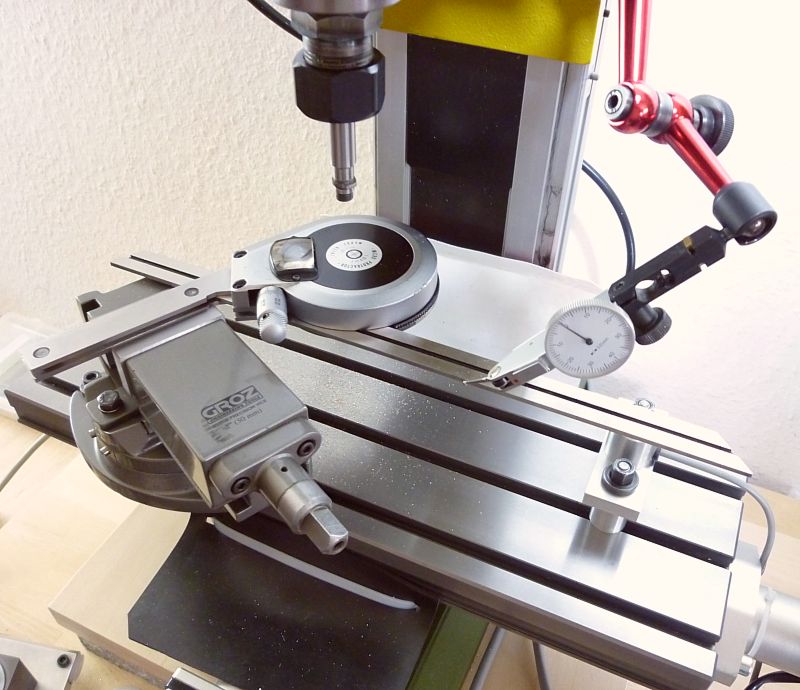
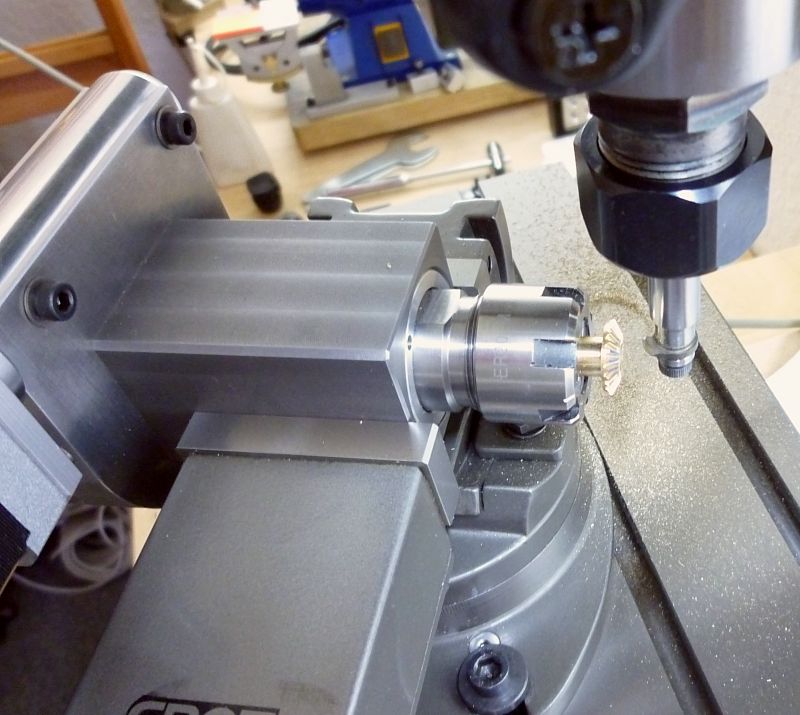
Und auch dazu gibt's natürlich noch zwei Videos:
24z Kegelrad Fräsen
12z Kegelrad Fräsen
Und hier die fertigen Kegelräder:

Das funktionierte schon recht gut, nur die Profiloberflächen sind, besonders am großen Rad, in
einigen Bereichen nicht perfekt geworden. Das liegt aber nicht am eigentlichen Fertigungsprinzip,
sondern an meinem Selbstbau-Modulfräser, in dem Fall war es der mit dem Profil für 24 Zähne. Den
hätte ich mir vor der Verwendung besser noch mal unter dem Werkzeugmikroskop angeschaut, dann wären
mir die leichten Macken im Profil vom Formdrehen gleich aufgefallen, so sah ich es leider erst in
der "brutalen" Vergrößerung am fertigen Zahnrad. In der Zwischenzeit habe ich mir einen Satz
m0.4er Modulfräser zugelegt, die nächsten Räder sollten also ne Nummer besser ausfallen....ha ha ha...
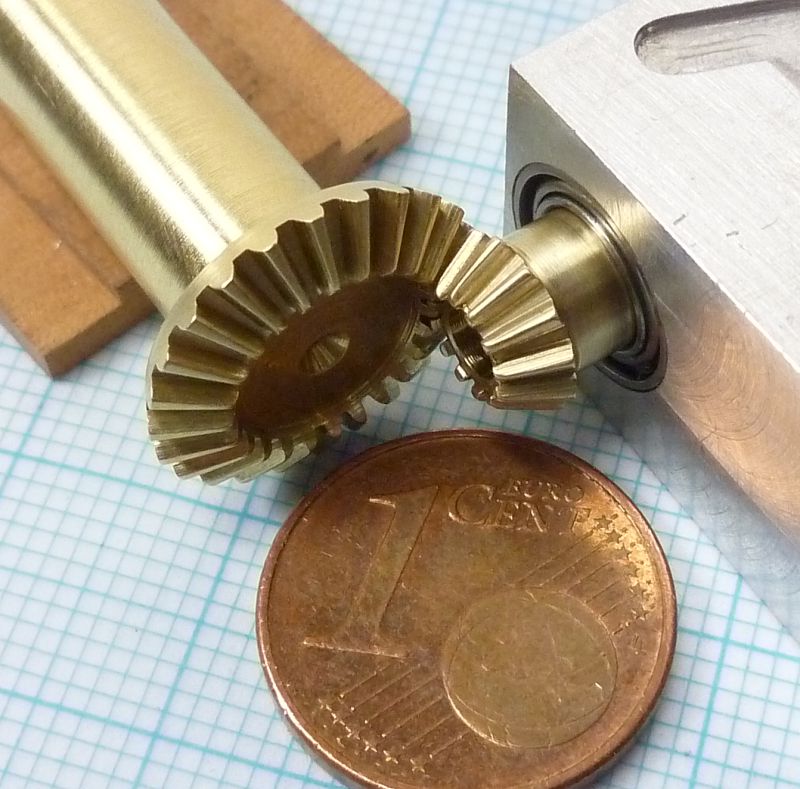
Im Test auf der Fräsmaschine zeigen diese Kegelräder schon jetzt ein saubres Laufverhalten. Ich habe sie dort längere Zeit mit Drehzahlen zwischen 5 und 8tausend Touren gequält, sie laufen durchaus ruhig und leise, jedenfalls auch nicht lauter oder gar hakeliger als meine vergleichbaren Räder aus industrieller Fertigung.
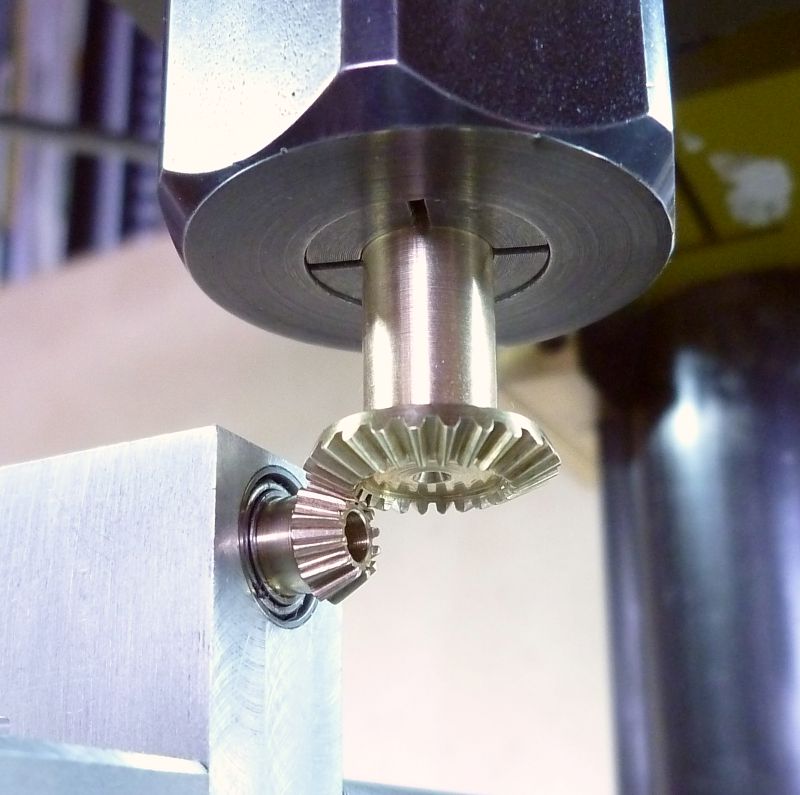
Tschüss vom Achim
|
|
| |